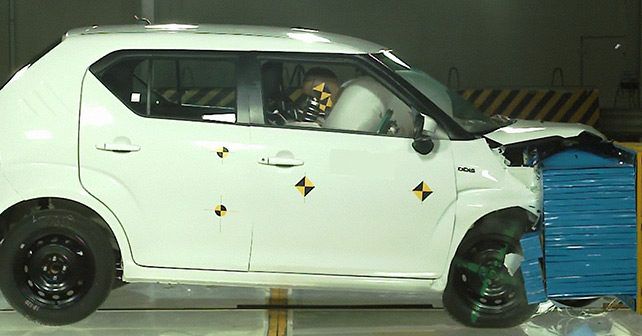
The 2017 Indian Car of the Year, the Maruti Suzuki Vitara Brezza, wouldn’t have existed it weren’t for Maruti’s new 600-acre R&D facility at Rohtak. Here’s an overview of this impressive facility after a highly anticipated visit.
When Maruti Suzuki finally issued a long-awaited invitation to visit their R&D Centre in Rohtak, little did I know that I’d come away with an in-depth knowledge of the human skeletal system – and specifically the femur and tibia!
This biology lesson took place at the one of the Passive Safety Labs at this mammoth facility – the pedestrian lab to be specific. This is where Maruti Suzuki tests its cars to ensure that they’re as safe as they can be, not only for the occupants but also for pedestrians in the event of an accident. The engineers – who sound like orthopaedic surgeons – test for every eventuality.
An Ignis is set up in one of the labs for our benefit. There’s a rig in front of it, which shoots one of two things at the front of the car – an orb that’s meant to resemble a human head and a cylindrical robotic leg of sorts that simulates the impact of a human leg against the front of the car. Maruti has the benefit of a great deal of crash test data from Suzuki, as well as various institutes from across the world, which point out that the two sources of serious injury in a crash with a pedestrian are 1) disability caused by the impact to the legs, following which the individual falls on the bonnet of the car and 2) risks fatal injury when his or her head eventually impacts the bonnet. In order to reduce the risk of either disability or fatality, Maruti tests their new cars to ensure that the front structure of the car absorbs a portion of the impact. They also ensure that there’s enough of a gap between the bonnet and the top of the engine so that the bonnet has the chance to deform and absorb the impact without hitting the inevitably solid engine block underneath.
When a new car is designed, the designers and engineers first perform CAE (Computer Aided Engineering) test simulations to ensure that their new models meet the specified guidelines (their own specifications tend to be more stringent than the regulations mandate). The engineers at Rohtak say that there’s a 90-95% correlation between the results that they see in the CAE tests and the physical tests that they perform in the lab – which means that the data that they’ve acquired is very accurate. The leg impactor has various accelerometers and sensors to measure the force of the impact and gauge the plausible extent of the injury. The leg is shot out of the rig at a very precise speed and trajectory onto a stationary car in a manner that perfectly simulates an accident. The lab is lit up by special flicker-free lights that ensure the entire test can be filmed at 1,000 frames per second by high-speed cameras. Among the various data points that the engineers acquire, they look at the flex between the knee, the femur and the tibia to determine the extent of injury – hence the in-depth orthopaedic knowledge. Who knew being an automotive engineer would require such a diverse skillset? And who knew the extent to which Maruti Suzuki tests its cars to be safe not just for its occupants but also for pedestrians.
Crash test regulations for frontal and side impacts come into force in India for new cars by October this year. Existing models have till 2019 to meet these regulations. Pedestrian safety regulations come into force for new models by 2018, and existing models by 2020.
Now, the engineers weren’t satisfied with merely denting the front of a brand new Ignis in the name of science. They wanted to absolutely destroy one – ostensibly for our benefit (and, of course, in the name of science). So, the next test we witnessed involved another brand new Ignis being hurtled towards a barrier at 56km/h. But before we got to see the crash test, we were taken to meet the sorry souls (fortunately already quite lifeless) who had volunteered to be the crash test dummies for the test. We were told that back in the day the industry used living and breathing crash-test drivers before these dummies were developed. They then moved on to using pigs because they wanted to crash cars at higher speeds – pigs, apparently, have a very similar tissue structure to humans. Crash test dummies were first developed in the aviation industry to test ejector seats, and subsequently first used by General Motors in the ‘70’s. Today, the entire industry uses a set of very sophisticated crash test dummies that are made by a company in the US. They are a little finicky though – firstly, they require a lot of calibration, and, secondly, they only perform at their best if kept at a constant temperature of around 22-degrees C. Talk about being demanding!
Well, I suppose they can afford to be since they cost anywhere between 30 to 80 lakhs per crash test dummy – depending on the type of articulation they can perform and what type of tests they have to endure. The side-impact and whiplash tests all require different sets of dummies. That being the case, perhaps they need to change their name to being crash test associates – dummies doesn’t quite seem apt.
At Rohtak, Maruti has an entire (extended) family of these crash test “associates” – in various shapes and sizes. The children are strapped into child seats. The engineers say that an unrestrained child in the event of an accident can accelerate up to 30-times its own weight. So, if the child weighs 10-kilos, in a serious crash that child becomes a 300-kilo projectile inside the car if not properly restrained. Think about that the next time you have your child in your lap, or you allow those sitting in the rear seats to leave their seat belts unbuckled.
All these crash test results are based on the assumption that every passenger will either be wearing a seatbelt no matter where they’re seated in the vehicle, and that children will be properly restrained in child seats.
In the test that we were about to witness, two full-size male “associates” had drawn the short straws. The test they had signed up for was a front-offset crash test. This meant that the front of the car would impact the barrier at exactly 56km/h on the driver’s side – to simulate a crash with an oncoming car on a single lane highway. It takes the engineers a couple of days to set up for such a test – which, effectively, lasts a fraction of a second. The car is pulled at a precise speed by a pulley. It’s released right before it hits the barrier. The barrier itself is designed to simulate an oncoming car with a similar crash structure – which means that a certain portion of the barrier also deforms and absorbs some of the impact of the crash. The barrier is attached to a solid concrete block weighing 90-tonnes. It’s so solid, in fact, that the control room sits on top of this structure.
Again, the crash is filmed from every angle – including below the vehicle to see how the underbody performs. All the fluids are drained and replaced with coloured water, so that the mess is easier to clean up presumably. Also, so that it doesn’t block the underbody camera – and, of course, so that the fuel doesn’t pose a fire hazard.
We kept our eyes peeled on the Ignis, as it charged towards its fate – looking distinctly like a lamb being led to slaughter. The front end of this car was than smashed and virtually destroyed in the blink of an eye. The violent forces of such a crash are truly evident when you see it unfold right in front of you.
The Ignis impacted the barrier and was thrown backwards – leaving behind a fair amount of debris in the process. We had to wait a few minutes for all the data to be acquired, and for some of the debris to be cleared, before we could get up close and personal with the car to assess the damage. The airbags fired of course, and filled the cabin with a certain amount of smoke. The first thing we noticed was that all four doors of the Ignis opened very easily afterwards – which was commendable indeed, considering the force of the impact. The passenger cell was completely intact, and the force of the impact was largely borne by the crash structure in front. The forces were then transmitted through the chassis via the A-pillars and through the floor – ensuring the integrity of the passenger compartment. Our crash test ‘associates’ got a face full of airbags, this much was evident, but would likely walk away from the scene of the accident. The driver’s right knee did hit the dashboard – we know this because he left some paint behind in the process – but would likely not have been seriously injured.
When you witness a crash such as this, and see how a modern car performs, it really is quite eye opening. The advances in safety are such that even the strut tower on the driver’s side – the side of the impact – was still intact. To say that the crash test – and the manner in which it was performed – was impressive would be a severe understatement.
In fact, to attempt to describe the scale and precision of this entire 600-acre facility would be an exercise in futility. You really do have to see it to believe it. Around the perimeter of the facility there’s a 5.8-kilometre high-speed track, which consist of two 2-kilometre straights, with two 35-degree bankings at each end. The banking could be built, and the asphalt laid, by one of only two companies in the world. In total, they have more than 30-kilometres of 30 different types of tracks at Rohtak – with every possible surface that you can think of.
Every car not only undergoes extensive testing for ride-and-handling, NVH and endurance, but – as we saw – crash worthiness as well. As many as 40 crash tests are conducted during the development phase of a new vehicle. The Vitara Brezza, for instance, was developed at Rohtak (as well as at Suzuki’s facilities in Japan) over a period of over two years. The Brezza was the first car developed by Maruti Suzuki in-house. But the engineering expertise to do so was built over three decades. Their journey started with localisation – building vendor capability –and enabling cost reduction.
Over the years, Indian engineers have been stationed with Suzuki in Japan for periods of time ranging from 6 months to 2 years in order to build up the understanding and know-how that’s led to the kind of development they undertake today. The first project undertaken was the facelift of the Zen in 2000. Following that, Indian engineers were stationed in Japan to work on the global model of the Swift and tune it for Indian road conditions. Subsequently, more than 100 engineers worked on the development of the Celerio. Engineering expertise and capability is developed in phases, and over time – and that’s exactly what Maruti Suzuki has done. After all, you have to know how to test a vehicle – and you have to know how to asses damage. With this knowledge base built up over decades, Maruti Suzuki can now do end-to-end development – from concept to execution – right here in India. And the Rohtak facility is key to this capability.
Construction started in 2011, and the company has so far invested 1,900 crores. A further 1,900 will be invested by 2019 – for a total of 3,800 crores. The facilities are state-of-the-art and cutting edge but not over the top and flamboyant like similar facilities that you may see in the West. The approach remains very down to earth, and it’s the results that count. The beneficiaries, in the end, are not only Indian car buyers but all road users – and the country as a whole. India’s love affair with Maruti is entering a new phase it seems – one backed by research and development!
Write your Comment