Interview with Prabhu Ramasamy, Head of R&D and Project Management (HBS), Continental Automotive India
Brakes are probably the most important component in a car and with Continental producing and developing key braking-related components right here in India, we spoke to Prabhu Ramasamy, Head of R&D and Project Management Hydraulic Brake Systems, Continental Automotive India to get some insights.
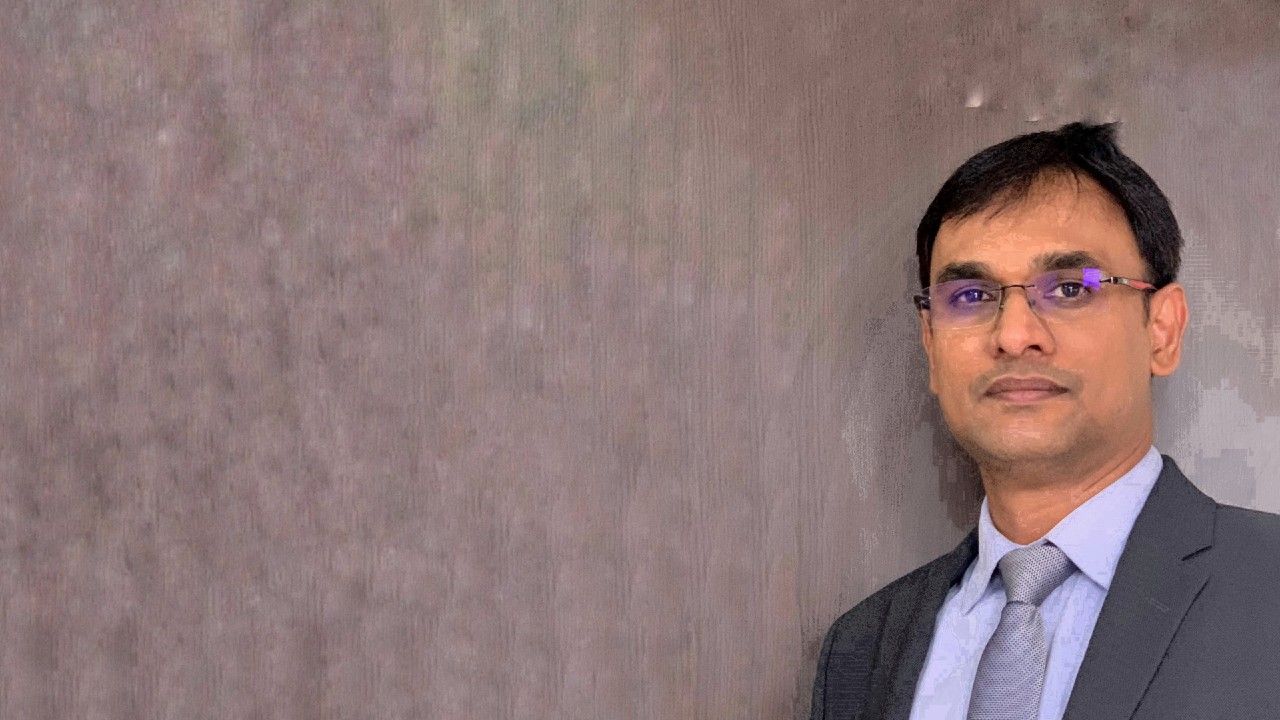
With Continental Automotive expanding its operations in India, we speak to Prabhu Ramasamy who heads R&D for HBS (Hydraulic Brake Systems) in India to get an insight as to what goes on behind the scenes when developing one of the most crucial components of a vehicle.
How much of the manufacturing process of brake systems is done in India?
Hydraulic Brake Systems are a part of our Safety and Motion (SAM) business area under the Continental Automotive Group Sector. We started our production of Hydraulic Brake Systems in 2008 – 2009 and now, we have 15 manufacturing plants all over the world, India being one of them. About 80 to 90 percent of the manufacturing process is done in India. We supply almost about 85 percent of our technology to the global market and 15 percent of it is supplied to the local market.
How much of R&D for new brake systems is done in India?
We have 10 research and development centers all over the world, including India. It is in Bangalore which is one of Continental’s largest R&D centers with over 4000 highly qualified engineers, supporting R&D for all automotive businesses of the company, both at a local and global level. They work on areas such as advanced safety technologies, autonomous driving technologies, and connected mobility. For existing products with upgradation or changes with respect to customer requirement and regulations, more than 95 percent of R&D is done in India. For new brake systems contribution from India, HBS R&D will see a significant increase in coming years and for the same we are building-up the team, competencies, and collaboration with global HBS R&D locations
Tell us some challenges in developing an HBS – for the Indian market
India is a cost sensitive market where the customers demand the best technology at affordable prices. As the Hydraulic Brake System technology is quite expensive, it gets a little difficult to cater to the demand of the Indian market. We at Continental follow the “In the market, for the market” approach where we try to provide the latest technology and mold it to satisfy the needs of the customers.
The second challenge that we face is the existence of competitors who have been serving the customers for a few decades with proven products. The customers rely on them as they believe them to understand their demands and needs.
What are some behind-the-scenes insights you can share with us?
Continental initially started manufacturing this technology for the local market but have recently expanded, serving the needs of the global market.
The various transformation deployment projects have made the Center at Bangalore the hub for R&D for Hydraulic Brake System. The R&D team which was present in Gurgaon till end December 2021 has been integrated with Bangalore - Tech Center India from January 2022 onwards.
The Technical Center enables us to get the right talents in the area of System Engineering, Software Engineering and new competencies for Autonomous Mobile Robot.
The Engineers support R&D for all automotive business of the company at a local and global level. This makes the Cross Business Area and Business Segment collaboration which is required for many new product developments in future.
Where do you see the industry going in 10 years?
The automotive industry is constantly evolving, and a significant change can be seen. The introduction of new technologies and policies has completely altered the structure and operation of the automotive industry. This revolution has been brought through digitization and various other technologies that are now being incorporated by the automotive industry.
Sustainability is one of the most important changes of all. Customers as well as the manufacturers prioritize sustainability. The manufacturers aim at producing technologies that are more sustainable at the same time serve the needs and demands of the market. The latest innovation by Continental, the Autonomous Mobile Robot for the agricultural sector has the potential to reduce the extensive use of chemical sprays and fertilizers which also helps with soil compaction, enabling sustainable increase in the yield of high-quality crops.
Earlier vehicles were considered just as a mode of transportation but due to digitization and connectivity, they have become much more. Vehicles have now become the mobile living space for consumers, providing both, comfort, and safety. Consumers expect seamless and personalized automotive experiences with the latest features. They are eager to participate in product and service innovation. The manufacturers are aware of this shift and are working on producing technologies that suit the changing consumer behavior.
The automotive industry is gradually transitioning from traditional vehicles to Electric Vehicle (EV). While the transition to zero-emission vehicles may take some time, EVs are unquestionably the more sustainable option with lower lifecycle emissions. Furthermore, the operating costs of EV operating are significantly lower than ICE engine operating costs. To encourage the use of electric vehicles, India has launched programs such as FAME I and FAME II, as well as various tax breaks. The benefits and government push have piqued consumers’ interest in adopting electric mobility.
As customers have started spending more time in their vehicles, it has become more than just a medium of transportation. Almost all vehicles now have connected devices of some kind. Automobile connectivity can be used for a variety of purposes, ranging from safety to comfort. Connected vehicles have the potential to change how we interact with our vehicles as well as how they communicate with the rest of the world. Cars must be connected in order to perform complex tasks and provide on-demand information that improves the overall driving experience. Smartphone integration has quickly become one of the most desired features among today's consumers.
With increased development and rapid growth, a major transformation is expected in the next ten years in the auto sector.
What are some key brake-related innovations that we’ll see in the near future?
The future brake system innovations continuously progress with the Hydraulic brake System Products and Electronic Brake System Products.
In addition to the Hydraulic Brake System and Electronic Brake System Products in future market will see Hydraulic/Dry Brake System that is Hydraulic in front and dry brake in rear and as a second step the complete front and rear may be fully dry brake systems. The coming years will see more regenerative braking in vehicles.
Drum brakes were popular earlier, but the industry moved towards disc brakes. But due to the popularity of Electric Vehicles, a revival of electric parking drum brakes can be seen. Electric parking drum brakes significantly reduce the dust emissions resulting in minimized particle emission. There are lesser chances of corrosion with encapsulated housing, ensuring an increased life span. Whereas the disc brakes have higher chances of corrosion because of less usage. The drum brake’s enclosed housing system allows the internal friction shoe, pully, and springs to operate reliably and perform to the required and relevant residual braking torque force application, while providing additional reliability for the instant and emergency case application.
The Brake system architecture is changing with Automated and electrification while posing new challenges to the existing brake system leading the way forward for eCaliper and eDrum.
Our “Vision Zero” will continue to drive our developments in safety technologies and to make safety available to everyone around the globe
Also read:
Experiencing safety technologies at Continental’s 2-Wheeler TechDrive
Write your Comment on